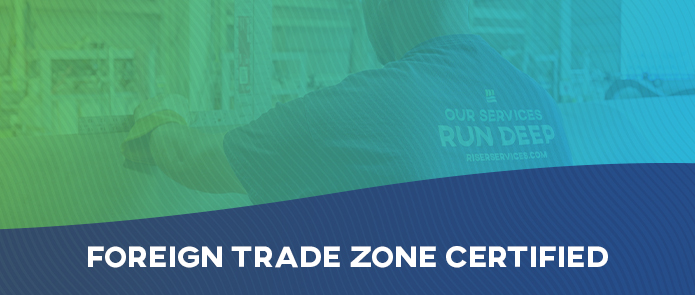
Your Solution to Eliminating Storage Tariffs and Duties
As a secure foreign-trade zone, its Houma storage facility is approved and certified to store drilling products without the need to pay customs or duties and property is not subject to ad valorem taxes. Providing cost-effective, turnkey storage services, the organization is poised to handle everything from transportation to logistics to ensure the customer’s experience is hassle-free.
“We are extremely pleased to share this news with our customers, industry partners, and prospective customers,” said John DeBlieux, Vice President of Deepwater Riser Services. “Our services span the full life cycle of the riser starting with our team delivering rigorous inspections, then focusing on critical maintenance, and offering convenient storage options that fit the needs of our customers.”
With 24 acres of dedicated storage and maintenance areas in Houma, LA Deepwater Riser Services offers a safe harbor and convenient access for transportation whether coming in or out of the Gulf of Mexico by truck or barge. Additional value is provided to importers who may be able to defer duties or tariffs on products by storing their items within the FTZ.
Deepwater Riser Service’s Houma storage facility is API Spec Q1 Registered and is located 15 miles off of Highway 90, which make it only a 1.5-hour drive from Port Fourchon and a 12-hour tow. To support its customers’ needs, the organization has additional facilities across the Gulf of Mexico that are strategically located to support the demands of the energy industry and allow their crews and vessels to be easily dispatched to support any operation internationally.
To learn more about Deepwater Riser Services’ newly certified Foreign Trade Zone and the advantages it can offer, please see here.
Foreign Trade Zone Advantages
- AVOID AD VALOREM TAXES Property stored within the FTZ is not subject to ad valorem taxes.
- CASH FLOW Inventory can be held in the FTZ without duty payment.
- EXPORTS In an FTZ, duties are simply never paid.
- INVERTED U.S. CUSTOMS DUTY SAVINGS The reduction or elimination of U.S. Customs duties can be significant.
- NON-DUTIABILITY OF LABOR, OVERHEAD AND PROFIT U.S. Customs duties are not owed on labor, overhead or profit attributed to production operations in an FTZ.
- REDUCED CYCLE TIME Delays relating to U.S. Customs clearances are eliminated.
- WEEKLY ENTRIES Weekly entry procedures can significantly reduce paperwork and expense.
- PRODUCTION MACHINERY Machinery for use in an FTZ may be assembled and installed before duties are owed on either the parts or finished product.
- INVENTORY CONTROL Operations in an FTZ require careful accounting of receipt, processing, manufacturing, and shipment of merchandise.
- ZONE-TO-ZONE TRANSFER A network of zone projects provides opportunities to reduce or eliminate duties.
- INSURANCE COSTS Cargo insurance rates should be reduced because imported merchandise is shipped directly to an FTZ.
- U.S. QUOTA Voluntary restraint and orderly marketing agreements are not impacted by FTZ use.
Location: 140 Industrial Blvd | Houma, LA 70363
This facility is API Spec Q1 Registered. From our headquarter location, we perform maintenance, inspection, repair and storage services for deepwater risers and subsea equipment. Located 15 miles off of Highway 90, it only a 1.5-hour drive from Port Fourchon and a 12-hour tow. Our additional facilities across the Gulf of Mexico are strategically located to support the demands of the energy industry. From these locations, our crews and vessels can be dispatched to support any operation internationally.
To find out how easy it is to take advantage of our newly certified Foreign Trade Zone, contact:
John DeBlieux, Vice President of Deepwater Riser Services
D:: 985.850.1226
C: 985.209.7568
jdeblieux@RiserServices.com
Recent Comments